Obróbka skrawaniem jest obecnie standardem w wielu dziedzinach przemysłu, a w szczególności tych obszarach, które wymagają wysokiej precyzji wykonania i minimalnych tolerancji.
Poza oczywistymi branżami – takimi jak przemysł lotniczy i kosmiczny czy automotive – produkcja sprzętu medycznego jest bardzo często realizowana przy pomocy urządzeń sterowanych numerycznie.
Toczenie, frezowanie (również zaawansowane 5-osiowe) CNC zapewniają wysoką wydajność oraz powtarzalną precyzję produkcji sprzętu medycznego.
Zastosowania technologii CNC w produkcji dla branży medycznej
Współczesna branża medyczna wymaga najwyższej możliwej precyzji i powtarzalności produkcji – dzięki tym cechom aparatura, narzędzia chirurgiczne czy części protez mogą być efektywnie (oraz komfortowo) używane zgodnie z przeznaczeniem.
Ratowanie zdrowia i życia czy poprawa ich jakości – to tylko kilka wartości, które byłyby trudne do zapewnienia przez współczesną medycynę gdyby nie niezawodne oprzyrządowanie czy akcesoria medyczne.
Z kolei rozwój technologii skrawania umożliwia precyzyjne wytwarzanie bardzo drobnych elementów – nieodzownych w wymagających i skomplikowanych procedurach medycznych, takich jak chociażby laparoskopia czy operacje neurochirurgiczne.
Obecnie zastosowanie produkcji CNC w sektorze medycznym widoczne jest m.in.:
- w wytwarzaniu narzędzi chirurgicznych, w szczególności ze stabilnych chemicznie stopów, takich jak stal (serie 200, 300, 400 i 500, a w szczególności stop 316L, najczęściej kojarzony „stalą chirurgiczną”),
- w produkcji mikronarzędzi, wykorzystywanych chociażby w laparoskopach – z racji wymaganej precyzji i powtarzalności zastosowanie maszyn CNC pozwala na spełnienie bardzo wysokich wymagań związanych z obróbką materiałów, kontrolą jakości (wejściowej i wyjściowej) i produkcją miniaturowych elementów,
- w wytwarzaniu części protez (kończyn czy zębowych), które wymagają wysokiej jakości wykonania oraz precyzyjnej obróbki – często niestandardowych – gwintów, niekiedy o niestandardowym skoku lub kształcie,
- w wytwarzaniu elementów większych układów – takich jak szkielety obudów urządzeń medycznych, takich jak tomografy czy rezonanse magnetyczne, często ze stopów niemagnetycznych,
- w produkcji części z tworzyw sztucznych – np. złączek z polimerów o wysokiej odporności chemicznej, które mogą być regularnie dezynfekowane przy pomocy agresywnych środków,
- w prototypowaniu – mimo tego, że technologia CNC umożliwia efektywną produkcję masową i pewnym wyzwaniem pozostaje optymalizacja kosztów w przypadku wytwarzania pojedynczych elementów, wiele firm z przemysłu medycznego wykorzystuje skrawanie numeryczne do produkcji pojedynczych obiektów (ze względu na precyzję) lub prototypów.
Innymi słowy – im bardziej wyspecjalizowane są konkretne akcesoria medyczne i wyższe wymagania, tym produkcja CNC lepiej sprawdza się w ich produkcji.
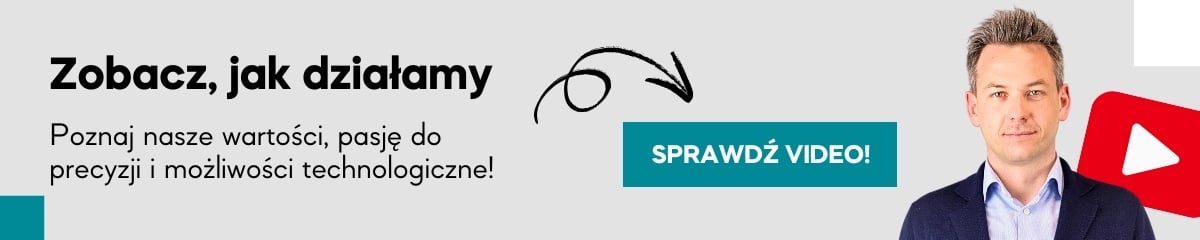
Korzyści z wytwarzania produktów medycznych przy pomocy obróbki CNC
Korzyści związane z produkcją opartą na CNC dla branży medycznej są zbliżone do tych, które sprawiają, że jest to standard w innych gałęziach przemysłu, takich jak branże automotive czy kosmiczna.
Zalety technologii CNC, które sprawiają, że jest to szeroko stosowane rozwiązanie przez przemysł medyczny, to m.in.:
- bardzo wysoka precyzja pracy – współczesne urządzenia CNC umożliwiają produkcję bardzo złożonych narzędzi i części, często zminiaturyzowanych, z zachowaniem skrajnie niskich tolerancji, które umożliwiają łatwą wymianę oraz precyzję operowania,
- wysoka powtarzalność i szybkość wytwarzania – technologia CNC pozwala na masową produkcję części, które (nawet przy zachowaniu bardzo skrupulatnej kontroli jakości) są niemal identyczne, dzięki czemu mogą być z łatwością wymieniane przy zużyciu i wciąż pozostawać integralną częścią większego układu,
- możliwość obróbki szerokiej gamy materiałów – stal to nie jedyny materiał stosowany w przemyśle medycznym. Współczesne centra CNC umożliwiają formowanie m.in. stopów metali, ceramiki, kompozytów czy polimerów,
- szerokie możliwości formowania – sterowane numerycznie urządzenia skrawające umożliwiają wytworzenie obiektów o niemal dowolnych kształtach. W połączeniu z procesami elektrodrążenia wgłębnego (EDM) mogą służyć do szybkiego i precyzyjnego wytwarzania nawet bardzo skomplikowanych obiektów,
- możliwość osiągnięcia stosunkowo niskiej ceny jednostkowej przy produkcji masowej,
- łatwość skalowania produkcji oraz wytwarzania nowej partii części/narzędzi (nazywana też produkcją na żądanie).
Materiały stosowane w obróbce skrawaniem dla branży medycznej
Branża medyczna kojarzy się ze stalą – jest to jeden z najstarszych znanych metali i używany powszechnie od zarania nowoczesnej medycyny. Dobre parametry mechaniczne sprawiają, że wykonywane były (i są wciąż) z niego ostrza czy instrumenty. Nie na darmo wiele osób kojarzy „chirurgiczną stal” z trwałością, precyzją i bardzo niskim ryzykiem wywołania reakcji alergicznej.
W tej grupie są najczęściej umieszczane cztery serie stopów żelaza z chromem, niklem, molibdenem i manganem o różnych proporcjach (200, 300, 400 500; seria 300 ma najwyższą odporność na korozję).
Obecnie jest to najczęściej stosowany materiał do produkcji narzędzi chirurgicznych, a nawet elementów protez czy „gwoździ” spajających kości. Dzięki bardzo wysokiej odporności chemicznej ten rodzaj materiału może być regularnie dezynfekowany (np. w autoklawach) i mieć stały kontakt z agresywnymi środkami czystości. Ta stabilność przekłada się także na niskie ryzyko wywołania reakcji alergicznej, nawet w wypadku stopów zawierających nikiel (dosyć często uczulający, co może powodować zagrożenie zdrowia w przypadku protez wewnątrzustrojowych).
Z perspektywy obróbki, rodzina stopów stali chirurgicznej charakteryzuje się dobrą skrawalnością i jest stosunkowo łatwa do formowania na zimno.
Rozwój metalurgii – jak i samej medycyny – sprawił, że do produkcji wielu narzędzi, w szczególności precyzyjnych, coraz częściej stosowany jest tytan, który zapewnia dużo lepsze parametry mechaniczne od stali, a zarazem – z racji wysokiej stabilności chemicznej – rzadziej może powodować reakcje alergiczne.
Tytanowe elementy – wykonane w technologii CNC – są często spotykane w protezach wewnątrzustrojowych (np. „tytanowa płytka w czaszce” lub „tytanowe gwoździe w biodrze”) czy precyzyjnych narzędziach chirurgicznych, np. służących do prowadzenia operacji neurochirurgicznych.
Z kolei szeroko rozumiany przemysł protetyczny (zarówno dotyczących protez wewnątrzustrojowych, jak i kończyn) powszechnie korzysta z polimerów, włókna węglowego, aluminium i tytanu. Są to materiały szeroko stosowane w nowoczesnej protetyce – dziedzina ta wymaga bardzo dobrych parametrów mechanicznych, które mogą pozwolić osobom korzystającym z takich urządzeń na powrót do normalnego poruszania się.
Lekkie stopy aluminium i tytanu, często obrabiane galwanotechniczne w celu poprawy odporności, wykorzystywane są do tworzenia elementów nośnych protez kończyn, a z kolei włókno węglowe, szklane czy polimery – to utworzenia korpusów.
Niskie tolerancje zapewniane przez technologię obróbki CNC instrumentów medycznych czy protez pozwalają na ich jeszcze bardziej efektywne wykorzystanie.
Z kolei dobór odpowiednich materiałów i właściwy montaż przekładają się na wysoki komfort oraz lepszą żywotność.
Prototypowanie medyczne i produkcja masowa
Obróbka CNC jest stosowana na całym świecie do wytwarzania sprzętu medycznego – w szczególności do produkcji masowej, również ze względu na możliwość wytworzenia identycznych części i precyzję.
Z drugiej strony rosnącą popularnością cieszy się druk 3D, w szczególności w szybkim prototypowaniu.
Ten sam projekt elementu, narzędzia lub całej protezy może być wykonany na drukarce przestrzennej jako prototyp, poddany analizie oraz przetestowany, a potem – w finalnej wersji – zlecony do masowej obróbki CNC.
Jest to coraz częściej realizowany proces, który pozwala na obniżenie kosztów prototypowania oraz znaczne przyspieszenie prac od pierwszych projektów 3D w oprogramowaniu CAD, aż do wykonanego z najwyższą precyzją elementu z docelowego materiału, obrobionego na skrawarkach sterowanych numerycznie.