Kwestie techniczne związane z obróbką na tokarkach – automatycznych, ręcznych i CNC – są określane zbiorczo terminem parametrów toczenia. Przekładają się one na czas niezbędny do wytoczenia elementu, jakość powierzchni, dokładność toczenia i zużycie ostrzy tokarskich.
Każdy z tych parametrów powinien być brany pod uwagę podczas pracy z tokarką – zarówno ze względu na uzyskanie oczekiwanej jakości wytworzonego elementu, jak i bezpieczeństwo operatora. Czym są parametry toczenia i jak wpływają na końcowy efekt tej formy skrawania?
Jakie są parametry technologiczne toczenia?
Podobnie jak w przypadku innych procesów skrawania, przed uruchomieniem tokarki – czy to tradycyjnej, czy to sterowanej numerycznie – niezbędne jest ustawienie parametrów jej pracy. Najważniejsze z nich to:
- prędkość obrotowa (n) – określa prędkość, z jaką głowica tokarki wprawia w ruch obrotowy zamocowany na niej blok materiału. Jest ona wyrażana w obrotach na minutę (obr/min. lub RPM – od angielskiego revolutions per minute),
- posuw (f) – określa przesunięcie noża w czasie niezbędnym do wykonania przez głowicę jednego pełnego obrotu. Wyraża się go w milimetrach na 1 obrót (mm/obr.). Jest on też niekiedy nazywany „posuwem roboczym”,
- prędkość posuwu (vf) – określa prędkość, z jaką ostrze porusza się wzdłuż obrabianego na tokarce elementu (ruch posuwisty),
- głębokość skrawania (ap) – określa głębokość, na jaką ostrze tokarskie wchodzi w obiekt, usuwając materiał (czyli: różnicę między średnicami powierzchni obrabianej a obrobionej). Ta wartość jest wyrażana jest w milimetrach,
- prędkość skrawania (vc) – określa odległość, jaką przebywa ostrze tokarskie w odniesieniu do obrabianego materiału w jednostce czasu. Wyrażana jest w milimetrach na minutę (mm/min.),
- moc (Pc) – określa moc niezbędną do skutecznego pokonania sił tarcia i efektywnego usuwania materiału przez krawędź skrawającą lub ostrze tokarskie. Wyrażana jest ona w watach i kilowatach,
- siła skrawania (Fc) – określająca siły oddziałujące na narzędzie skrawające i przedmiot obrabiany,
- moment obrotowy (Mc) – wyrażany w niutonometrach (Nm).
Innym parametrem, niekiedy traktowanym jako podległy prędkości posuwu, jest czas maszynowy toczenia (wyrażany w minutach). Określa on to, jak szybko usuwany jest naddatek materiału z powierzchni obrabianego przedmiotu. Uwzględnia m.in. parametry takie jak:
- długość przejścia narzędzia,
- prędkość posuwu,
- prędkość obrotową,
- liczbę przejść narzędzia skrawającego wzdłuż powierzchni obrabianej.
Parametr ten pomaga określić, jak szybko poddany procesowi toczenia przedmiot uzyska
oczekiwany kształt lub zakończony zostanie etap obróbki (zgrubnej, kształtującej lub
wykańczającej).
Pomaga on efektywniej wykorzystać czas pracy narzędzi, a w przypadku tokarek CNC –
określić dosyć precyzyjnie czas niezbędny na realizację konkretnego etapu pracy.
Każdy z tych parametrów pomaga na lepszy dobór rodzaju obróbki.
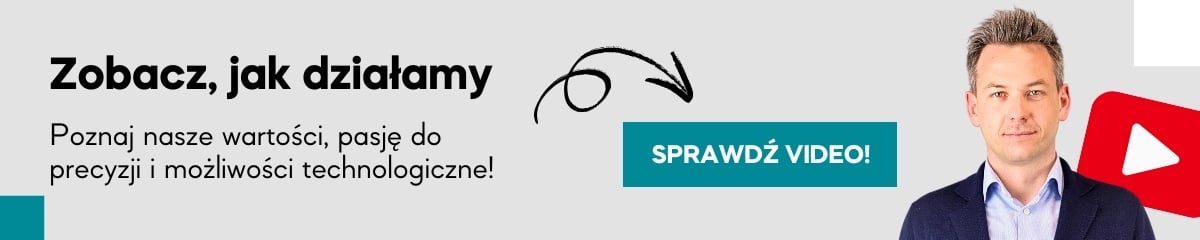
Jak dobrać parametry toczenia do obrabianego materiału?
Kluczowym krokiem przy doborze parametrów toczenia jest znajomość właściwości obrabianego materiału. Odpowiednie ich ustawienie przed rozpoczęciem pracy jest bardzo ważne ze względów bezpieczeństwa operatora tokarki, jak i efektywności pracy.
Doświadczony specjalista powinien dobrać odpowiednie parametry toczenia m.in. ze
względu na:
- rodzaj obrabianego materiału i jego właściwości fizyczne,
- ogólną skrawalność konkretnego materiału (z uwzględnieniem twardości charakterystycznej czy grup materiałowych ISO),
- zastosowaną krawędź skrawającą (noże czy wiertła tokarskie, dobrane do pracy z konkretnym materiałem i pozwalające na osiągnięcie oczekiwanej głębokości czy efektywności skrawania),
- warunki obróbki (np. jakość materiału obrabianego, brak wad odlewniczych i kuźniczych czy stabilność zamocowania obiektu toczonego na głowicy),
- parametry pracy tokarki,
- etap obróbki.
Dobierając parametry operatorzy tokarek często posiłkują się już zebranymi danymi – tzw. „pierwszym wyborem z katalogu”. Pomaga to usprawnić pracę oraz określić wstępne wartości – czy to dotyczące samego toczenia, czy też doboru odpowiednich narzędzi.
Obliczanie parametrów skrawania podczas toczenia, na podstawie obserwacji obrabianego materiału i pracy urządzenia, takich jak posuw roboczy czy inne parametry obróbkowe, pomaga ustalić docelowe wartości.
Warto dodać, że w przypadku pracy z tokarkami automatycznymi, wymagającymi ręcznego sterowania, parametry toczenia regulowane są najczęściej przez operatora, na podstawie danych katalogowych, doświadczenia oraz obserwacji procesu skrawania.
W przypadku tokarek CNC ogromnym wsparciem są systemy CAM, pomagające w określeniu odpowiednich parametrów pracy. Dodatkowo – dzięki zbieraniu danych przez różnego rodzaju czujniki – mogą modyfikować parametry pracy tak, aby jak najlepiej zrealizować proces toczenia sterowanego numerycznie.
Obróbka zgrubna, kształtująca czy wykańczająca - jakie parametry toczenia dobrać?
Proces obróbki skrawaniem – niezależnie od tego, czy jest to frezowanie, toczenie czy szlifowanie – dzieli się na cztery kluczowe etapy:
- obróbkę zgrubną (wstępną), nastawioną na usunięcie nadmiaru materiału i uzyskanie zbliżonego kształtu obiektu,
- obróbkę średniodokładną, skupioną na nadaniu obiektowi obrabianemu wstępnego kształtu,
- obróbkę dokładną (czasem nazywaną „precyzyjną”), nastawioną na nadanie obiektowi finalnego kształtu,
- obróbkę bardzo dokładną („wykańczającą”), w trakcie której usuwane są z powierzchni obrabianego obiektu ślady po przejściach krawędzi skrawających. Najczęściej jest realizowana przy pomocy narzędzi ściernych (np. szlifierek CNC i automatycznych).
Oczywiście: w zależności od obrabianego materiału czy oczekiwań wobec jakości powierzchni tych etapów może być więcej (jak w liście opisującej parametry różnych etapów toczenia poniżej).
Każdy z nich wymaga zastosowania innych parametrów toczenia, a niekiedy też różnych rodzajów ostrzy czy wierteł tokarskich. Również oczekiwania wobec jakości uzyskanej powierzchni są różne – o ile przy obróbce zgrubnej wyraźne ślady narzędzi skrawających są normalne, o tyle takie ślady po obróbce bardzo dokładnej czy dokładnej świadczą o złym doborze parametrów lub krawędzi skrawającej.
Zakładając poprawność doboru narzędzia do rodzaju toczonego materiału, na różnych etapach obróbki zaleca się zachowanie następujących parametrów toczenia (odpowiednio dla posuwu roboczego i głębokości skrawania):
- obróbka bardzo zgrubna: >0,7 obr/min / 8-20 mm,
- obróbka zgrubna: 0,5-1,5 obr/min / 6-15 mm,
- obróbka lekko zgrubna: 0,4-1 obr/min / 3-10 mm,
- obróbka średniodokładna: 0,2-0,5 obr/min / 1,5-4 mm,
- obróbka wykańczająca: 0,1-0,3 obr/min / 0,5-2 mm,
- obróbka bardzo dokładna: 0,05-0,15 obr/min / 0,25-2 mm.
W dużym skrócie: im wyższa precyzja, tym toczenie powinno odbywać się wolniej.
Dobór parametrów skrawania przy toczeniu obrabianego przedmiotu a zużycie ostrza
Dobór odpowiednich parametrów toczenia ma bezpośredni wpływ na żywotność narzędzi tokarskich. Poza typowym dla każdego ostrza zużyciem (ścieraniem) mechanicznym, które następuje w wyniku obrabiania powierzchni nawet przy doborze idealnych parametrów skrawania, są powody, które wpływają na jego przedwczesną utratę właściwości. Są to:
- adhezja – czyli nagromadzenie się na ostrzach „narostu” z obrabianego materiału. Obniża ona efektywność pracy (niechciany materiał pokrywa krawędzie skrawające, a co za tym idzie – to one mają kontakt z powierzchnią obrabianą), a dodatkowo wpływa negatywnie na jakość powierzchni. Problem ten pojawia się najczęściej przy zastosowaniu zbyt niskiej prędkości skrawania,
- utlenianie i dyfuzja – czyli osadzanie się na krawędzi skrawającej, w wyniku oddziaływania wysokiej temperatury, atomów obrabianego materiału. Powoduje obniżenie efektywności toczenia i może bezpośrednio wpłynąć na wcześniejsze stępienie narzędzia. Pojawia się najczęściej przy doborze zbyt wysokiej prędkości toczenia lub braku odpowiedniego odprowadzania ciepła i / lub chłodzenia obrabianego obiektu.
Dobór odpowiednich parametrów skrawania czy narzędzi podczas toczenia – CNC czy tradycyjnego – jest kluczowy zarówno dla efektywności, jak i jakości pracy. Doświadczeni operatorzy tokarek z łatwością dobiorą właściwe wartości – dostosowane do materiału czy precyzji wykończenia toczonej powierzchni.
Toczenie CNC - usługa, którą wykonujemy z pasji i z doświadczenia.
W RADMOT produkujemy na najnowocześniejszych maszynach, wprost od renomowanych producentów (m.in. Fanuc, Okuma, DMG, Hermle). Nowoczesny park maszynowy CNC oraz doświadczony zespół pozwala nam produkować szerokie portfolio różnych części. Oferujemy zarówno usługi frezowania CNC, usługi toczenia CNC, jak i wiele usług dodatkowych, w tym mycie, anodowanie aluminium, znakowanie laserowe oraz montaż.
Skontaktuj się z nami i powiedz, czego potrzebujesz. Usługi CNC świadczymy od niemal 40 lat. Nasza wycena jest zupełnie darmowa. A jeśli będziesz mieć wątpliwości, jaka technologia sprawdzi się u Ciebie najlepiej, doradzimy Ci na każdym etapie procesu.