CNC technology – in other words: computer numerical control – is one of the most important revolutions in the area of manufacturing and materials processing. Introduced in the 1950's sped up the manufacturing of large quantities of parts and allowed for a decrease in the unit price of many final products. Thanks to that development access to many goods – so far luxurious, like cars – became easier.
After almost 70 years after the introduction of said technology, CNC machining remains one of the "keywords” many people still connect with modernity, the modern manufacturing industry, and cutting-edge technologies.
And although each of these statements is true, CNC machining itself remains way more complex and still a developing area of manufacturing. After the first CNC mills and lathes, the industry developed much more complex devices (eg. 5-axis mills, waterjets, or laser cutters).
What is CNC technology and what are its main applications?
CNC – often called the "CNC technology” or "Computerized Numerical Control” (thus the CNC acronym) – is a form of automatized control of the machines and other manufacturing devices by a computer (today: microcomputer; earlier – perforated cards), used mainly in the machining and production of many types of parts.
Step 1 |
The CNC controllers send G-Code commands to the executive devices (eg. CNC lathe) in a structured form.
The G-Code itself is a normalized language of commands for numerically controlled devices. Said communication allows to achieve high precision of machining and creates a foundation for the repetitive manufacturing of high-quality parts with minimal tolerances.
Although said precision depends on the machined material and device calibration, the top-tier precision level of CNC machines is around 0.01 mm (approx. 0.000394 in).
Bear in mind even the most precise device is not self-controlled and requires knowledge and experience in programming.
⏳ Little reminder |
Said commands are often a form of translation of the CAD file (computer-assisted design software, eg. AutoCAD or SolidWorks) project to the computer-aided manufacturing (CAM) – software.
Step 2 |
The next step is testing – not only for errors in the CNC program itself but during prototyping.
Step 3 |
And the last step of CNC-based manufacturing is the preparation of the logistics of that process.
All of these steps can and usually take a lot of time. That is why CNC manufacturing is a perfect solution for the mass production of parts. |
One-of-parts production is way below the profitability level, which is why for the production of small batches automatic mills or lathes are still the way to go. Although less efficient, is perfectly suited to produce scarce parts (eg. turning individual pins or milling a small number of plastic objects).
The threshold of profitability depends on the project, but over 50 – sometimes even 20 – parts CNC machining can be a better solution, especially due to its higher precision and repeatability. Said cannot be achieved even with the usage of the best automatic devices, templates, and professional quality control.
In addition, CNC-based production of batches of parts can be quicker and more agile. Over that 50-ish threshold, CNC manufacturing remains the best solution for almost every (if not every) industry.
Many companies focused on outsourcing CNC services have a general "level of profitability for customer” (in RADMOT we often use a quantity of 100 parts in a batch), but everything depends on the project itself.
Want to work with experts in CNC field? 💪🏻 We analyze each project individually and try to approach our customers |
Another area where CNC machining shows its potential is the production of complex parts from one block of material (eg. forged aluminum, like some engine blocks).
And although CNC technology for years focused on 2D machining, recent decades show a strong leap into more complex technologies like 5-axis mills (and even more complex) that allows fast machining of even more complex objects and parts.
Said machines enable the production of complicated parts on one table, with maintaining the tightest tolerances and decreasing human error during moving blocks of material between worktables. Multi-axis mills allow increased precision, smoother operation in all axes, and overall: faster production. That type of manufacturing – with similar speed or precision – would be impossible without computerized numerical control.
To sum up – the utilization of CNC technology in manufacturing allows to:
reduced cost of a manufactured unit |
faster production |
higher repeatability of manufactured parts |
increase in margins for a client |
decreasing tolerances of produced parts and objects that have a positive impact on their longevity |
optimization of logistic processes is incredibly important in many industries, like automotive |
The history of CNC technology - in the nutshell
The history of the development of CNC machining begins in the 1950s in the USA 🇺🇸.
Technology has its roots in contract from the US Air Force and was developed in cooperation with the well-renowned Massachusetts Institute of Technology (MIT).
👉🏻 The goal was simple: to provide high precision and repeatable part manufacturing – the key requirement in the production of jet plane engines (back then: the cutting edge technology), while maintaining the highest precision of production to achieve the best possible balance of elements. |
First CNC machines were called "NC” (numeric control) and their operation was controlled by programs punched in the perforated cards (ancient technology, in the 1950s – the most advanced).
With the development of computer technology and the arrival of the first microcomputers in the 1970s and 1980s, said machines became a "computerized numerical control”.
CNC technology – at its full potential – was born.
Thanks to that development CNC provided even higher precision, repeatability, and ease in managing the whole manufacturing process. There was no need to prepare perforated cards and the whole programming process could be performed in one device – (micro)computer.
Other leaps were an increase in the operating memory of devices and the development of a "kinetic” part of CNC machining (eg. faster-moving speeds or better stability in high RPM).
Those changes made whole processing faster, and more precise and the device itself can manufacture higher quantities of parts while maintaining the tightest tolerances.
It is with mentioning the invitation and development of CNC technology is often mentioned as one of the biggest milestones in the 3rd and 4th industrial revolutions. Technology itself had and still has a significant impact on our society and the overall increase of living quality all over the world.
Applications of the CNC t
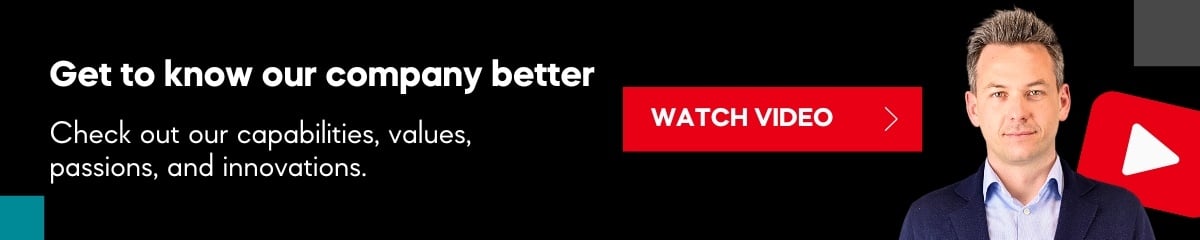
CNC devices (mills, lathes, lasers, etc.) are used currently in almost every industry focused on the production of parts or other elements. The key advantages of that technology are strong indicators of – almost overnight – becoming an industry standard.
Among these we can highlight the following:
- impeccable precision of manufacturing parts,
- high speed of production of large quantities of elements,
- high repeatability,
- intuitive control (especially for experienced CNC operators),
- a vast variety of applications – from typical machining devices like mills, lathes, or sanders/grinders, to lasers or waterjets – that allows to produce and finish of parts of almost any shape or made of any material,
- decrease of unit cost in mass production.
Currently, CNC machines dominate in manufacturing processes like:
metal machining (eg. steel, aluminum, brass, titanium) | polymer machining (eg. POM, acrylic glass) | wood machining | other material machining, like epoxy resin |
CNC machines allow fast and agile manufacturing of parts for many industries like following:
- automotive industry – from drivetrain parts (engine blocks and heads or gearbox housings), through the manufacturing of the body elements, to the production of the small interior parts (eg. consoles made of polymers),
- aviation industry – from the engine parts (that require very high precision and machining hard alloys like titanium or high-performance aviation aluminum) to interior parts (eg. cockpit elements),
- energetic industry – eg. manufacturing parts of the transformers or racks,
- computer industry – eg. precise machining of computer parts, racks, or CNC-driven soldering processes,
- production industry – manufacturing a vast variety of bigger and smaller machine parts and devices (eg. pins, gears),
- space industry – just like aviation requires the highest precision of production, utilization of very high-performing alloys, and tightest tolerances,
- bike industry – from the bike frames to small parts of the drivetrain like gears,
- medical industry – medical instruments or clinic equipment is usually manufactured with the utilization of CNC machines,
- furniture industry and everything we can call "home decor” – furniture, decorative elements, and others are usually manufactured in CNC devices due to mass production requirements and advantages of said technology. Even in woodworking.
As you can see: the utilization of advanced CNC machines is visible in almost every contemporary industry. The numerically controlled devices have a strong impact on the decrease of unit cost, longevity, and better availability for the end customers.
How do the CNC machines work?
CNC machines – that term can suggest the complexity of said devices.
And… that is true: said machines are complex and require good knowledge in many fields.
From the perspective of people who are not aware of "how the CNC machines work” the easiest way to answer is:
|
In other words: CNC devices control the work of known machining devices to decrease the possibility of (human) error, like during hand-driven milling, even with a perfect template, that can lead to the production of flawed parts.
The key aspects of the CNC machine's work are:
proper maintenance, calibration, and maintenance of machines | usage of proper techniques, speeds, and cutting tools (eg. cutters, bits, blades, grinding discs) | the right preparation of the work (in other words: programming), and – if needed – prototyping and testing the whole program before launching mass production |
Said features make CNC manufacturing fast and smooth, but the preparation of it is time and labor-consuming. That is why one of the key parameters of CNC-driven production is profitability level.
Preparation of manufacturing even simple parts can take time – that is why said "level” is usually consulted with the client in answer to a quote.
In RADMOT we estimate said quantity around 100 per batch, but every order is different which is why – in some situations – said level can be even lower. Our operators and customer service is focused on delivering the highest quality answers for our clients – that is why we analyze each order individually, with the customer's interest in mind.
The best technology, professional CNC operators - that is the core of our business
At RADMOT, we offer CNC milling services, CNC turning services, as well as many additional services, including washing, aluminum anodizing, laser marking and assembly. We have at your disposal over 80 modern machines in our machine park, all from renowned manufacturers. Download the presentation and check on which machine tools we produce CNC turned parts and CNC milled parts.
Contact us and tell us what you need. We have been providing CNC services for almost 40 years. Our valuation is completely free. And if you're in doubt about which technology will work best for you, our expertise is at your service.