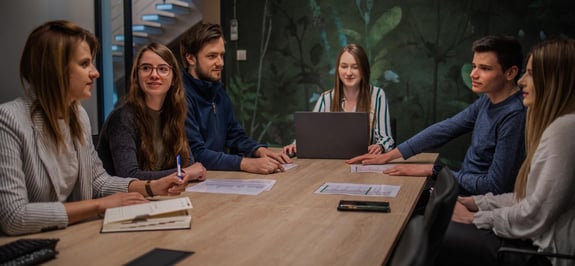
About us

WHY US
Benefits of cooperation
As CNC company, since we are in possession of over 80 machine tools, we can match a perfect machine with a given part and quantity in order to provide for competitive price
Why should you trust us?
- 01 Quality
- 02 Flexibility
- 03 Long-term cooperation
- 04 Competitiveness
- 05 Professional competence
Our certificates and diverse industries we have been active in for almost 40 years may serve as the best proof of our highest standards and quality. But that is not all. In order to be able to support our partners comprehensively, we attach great weight to additional services, which are part of our CNC solutions.
We can offer the following additional services:
surface treatments laser marking assembly works washing technical assistance.
We also co-operate with our reliable partner companies in the area of anodising, galvanising, blackening, and many other services.
Is your product portfolio extremely wide? Great! We can allocate the production of your parts among several machines that correspond to the particular parts you need.
Are you looking for a manufacturer of only one specific part? As the CNC company we can also deal with this on the A to Z basis.
Due to our flexibility, we can offer competitive prices and select the right technology for a specific part. In case any problems occur, we have many machines to use in order to meet our deadlines. We work according to the motto: “Many roads may lead to Rome, but only one of them is the right one”. It is thanks to this attitude, which we have worked out over the past years, that we are able to follow the optimal path.
What mainly matters to us mutual trust and common commitment to reach the objective we have identified at the very beginning of cooperation. By working together do long, we are able not only to understand your company better, but also to always be one step ahead of your competitors.
Each business of each our Customer is treated by as if it was our own business. By using this approach, we can constantly improve and control our process, and, in consequence, produce our parts on time and without any unpleasant surprises.
We are not the cheapest on the market. Obviously, we can explain it with reliability or confidence that your parts will be delivered on time and with no surprises. Nevertheless, this is just one side of the coin. What is important for us above all is a successful cooperation, and we believe that it is from this that our prices are derived.
CNC company RADMOT:
- Best specialists on the market
- State-of-the-art machines
- Well-known brands in our portfolio
- Certificates
- Approach towards each Customer service
We always take a holistic approach to your enquiries. We focus on all stages and requirements of the project. What stands behind this approach is years of experience in project management, expertise in CNC machining, and working in compliance with ISO and IATF standards. Equally invaluable is the support we receive from the wide base of our sub-suppliers.
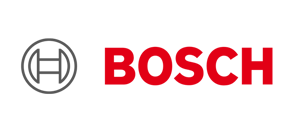
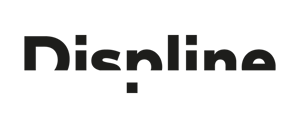
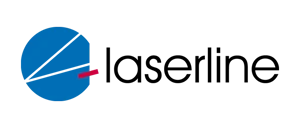
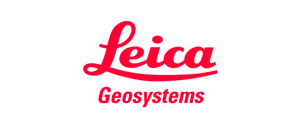
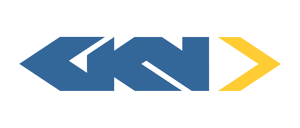
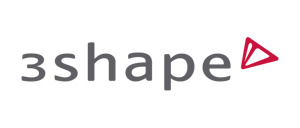

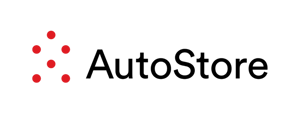
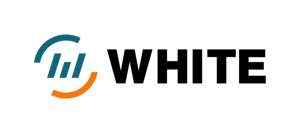
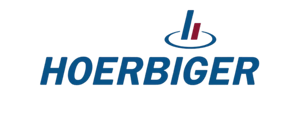
Sounds interesting? Get a free quote!
You can count on a competitive price, which you can easily break down and know what you are specifically paying for.
- Management Board
- Sales Department
- HR Department
Mission
Mission
Customer - cooperation with our Customers is based on partnership, involvement, and reliability.
Our team - we provide our personnel with safe and stable conditions of work, as well as constant development opportunities.
Solidity - we offer high level of service and the most appropriate technological solutions. We complete our orders on time and in the highest quality.
Values
Values
We act in accordance with the highest business standards - we handle our Company’s resources and the natural environment in the sustained manner.
We offer the highest quality of services - we launch innovative solutions, and we build our relations based on trust.
We create a special work environment for special people – we are not hierarchical, we motivate our personnel to work with full involvement so that we can develop together.
CSR
CSR
For our employees - we strive to provide stable working conditions, ensure that our company is a friendly place to work, provide extensive development opportunities and a good family atmosphere.
For young people - we participate in the dual training of students from technical schools, every year we take on a dozen or so technical students and students for internships, we are involved in the promotion of industry among young people in the region.
For the community - we support local actions and initiatives, invest in sports teams, sponsor regional events and happenings, engage in charity work.
Find out more about the principles of cooperation
We realise that clarity and transparency are key to building trust and effective cooperation. That is why we have decided to compile and make available a collection of the most important information that you may encounter when considering or starting a cooperation with our company. We hope that they will help you to understand what cooperation between our companies may look like.
At the same time, we understand that every project is unique and brings with it specific requirements and expectations. Therefore, in addition to general information, we aim to provide detailed explanations of the technical aspects of CNC machining, available materials, personalisation options and customisation.
Our aim is not only to present our capabilities, but also to show how we can work together to realise projects that go beyond standard solutions.
How long will I have to wait for a quote?
We know how important time and clear rules of cooperation are in business, which is why we pay special attention to ensure that our customers are comfortable with both. After sending your enquiry, you will receive an immediate email confirmation from us. Within the next 3 days, we will pre-assess our ability to undertake production. After this time, expect to be contacted by email or telephone from your company's assigned dedicated Project Manager. Direct contact is the basis for us on the way to preparing a satisfactory, attractive offer. Depending on the complexity of the project, a quote should be ready within 5 days.
Who will take care of the day-to-day cooperation?
Every quote we receive goes straight to a dedicated Project Manager. This will be the person with whom you will be in constant contact and who will oversee the progress of the quote as well as the delivery of the order. However, we have an entire project team working on every enquiry we receive, which includes:
- Technologist- Buyer
- Quality Engineer
- Production manager
In the case of complex orders, we involve further people from the ancillary services or warehouse departments for individual labelling and packaging.
Can I make an appointment at the company's premises?
If you only feel like it then don't hesitate to contact us to make an appointment! Our Project Managers work stationary from 8:00 a.m. to 4:00 p.m. We are open for visits from our clients and external audits. See you there!
Do you offer assistance in designing parts for CNC machining?
We design the technology, cutting tools and measuring fixtures necessary to make a part. However, there are occasions when we suggest minor changes to the design of the part itself, for example:
- optimise the efficiency of the manufacturing process,- to ensure the required tolerance,
- reduce costs resulting from the preparation of specialised tools.
What are the approximate lead times for CNC machining orders?
The lead time for an order depends on the specifics of the order in question. The calculation of the lead time already begins at the stage of determining material availability. We have a network of reliable suppliers and specialists proficient in the procurement of CNC machining materials. Our advantage is that we have up to 85 CNC machines at our disposal and work in three shifts. We are also good at predicting the time required for a given process, and we manage the work of individual machines and operators centrally on our IT systems. This allows us to offer reliable and attractive lead times.
Model lead times are:
- New orders from 6 to 12 weeks - depending on the number of external processes and the need for special tools)- Batch renewals from 4 to 7 weeks - depending on the number of external processes and batch size
The deadlines in each case also depend on the workload on the machine park.
What is the quality control process in CNC production?
We carry out the quality control process at every stage of the production cycle, and we start by controlling the quality of the material to be machined. Then, we closely monitor the achieved parameters of the workpieces after arming and producing the first pieces. For this, we use optimally selected measuring machines, of which we have as many as 22 types in the laboratory. The work culture of our Operators, who are particularly trained to understand and carry out spot checks during production, is also not without significance. For the most demanding customers, we can carry out a final inspection of 100% of a given production batch. We are ready to meet the requirements in accuracy class 6.
Does RADMOT offer a comprehensive manufacturing process from material selection to delivery?
Yes. We rely exclusively on proven partners for the supply of high-quality materials as well as proven suppliers of additional services. Due to our extensive measurement facilities and extensive quality control processes, we take comprehensive responsibility for the quality parameters of the orders we accept, regardless of whether they are carried out in cooperation. The same applies to the network of safe and fast shipping companies with which we work closely. Our experience spans 40 years, so we are no strangers to any aspect of our customers' expectations. On the other hand, we are open to producing on entrusted material and relying on transport organised by the customer.
How does RADMOT protect the customer's intellectual property?
Our company has experience of working with global brands. We have already been entrusted with the production of even high-value prototypes. It goes without saying that we sign NDA (non-disclosure agreement) agreements with our customers under the terms specified by the customer in question. These oblige us not to disclose confidential information, whether technical or, for example, the negotiation process and contract terms, under penalty of a fine.
What are the procedures in the event of non-compliance with customer requirements?
Information about complaint and error correction procedures is important for building trust between customer and supplier. As we work for the automotive industry for this purpose, we use, for example, the 8D Report extended by the Ishikawa and 5Why model to fully analyse the root cause of non-conformity. This is currently the most effective method to comprehensively manage non-conformity.This methodology in the industry was spread by the Ford corporation and then taken up by all major ‘players’ in the business.
In the case of complaints, the 8D report is the generally accepted standard but we also use it to resolve problems:
- Ishikawa diagram https://en.wikipedia.org/wiki/Ishikawa_diagram
- 5Why + 2 How https://en.wikipedia.org/wiki/Five_whys
- Problem Solving https://en.wikipedia.org/wiki/Problem_solving
Of course, we have all this described in internal procedures that meet the standards of ISO 9001 and IAFT. In preventive situations, we use FMEA to assess and prevent risks; it is worth mentioning that our company had extensive training in the new FMEA approach last year.
Of course, we have all this described in internal procedures that meet ISO 9001 and IAFT standards. In preventive situations, we use FMEA to assess and prevent risks; it is worth mentioning that our company had extensive training in the new FMEA approach last year.
In addition, if deviations from customer expectations are detected already at the production stage, products are stopped with us and the situation is discussed in detail with the customer. A product that does not meet 100% of the requirements can only be sent to the customer by prior arrangement - this is a requirement of the standards and of our customers.
Do you support optimisation of the project in terms of production costs?
During the analysis of each incoming enquiry, our design team assesses the technological feasibility of producing the part. It is common that the results optimise proposals, not only to reduce production costs, but also, for example, to suggest changes to the geometry that will not alter the usability of the part. Because we have extensive measurement facilities and specialise in precision production, we sometimes suggest changes in the approach to certain tolerances. All in order to be able to produce a given order as cheaply and as quickly as possible.
Do you have additional questions or need more detailed information?
-
2023 - 2024
The last two years have seen investment in a further production hall (DP5) and the launch of our own Anodising Plant. All this in order to take an even more comprehensive approach to the orders.
-
2015 - 2022
We have expanded up to a point where we now employ more than 200 persons and own almost 90 state-of-the-art CNC machine tools. In 2022, we started a new hall.
-
2014
We built a new hall dedicated to the automotive industry, and launched a serial production of power transmission parts, commencing our long-standing cooperation with GKN Driveline Company.
-
2002 - 2013
In 2002, we moved the production to our newly-built headquarters in Wola Gutowska, in Jedlińsk near Radom. The following years meant hard work in gaining experience, new markets and new Customers, and constant development of the Company.
-
1997 - 2001
In the following years, we continued to invest in new machines and to launch production for successive sectors, including machine, electrical engineering, and optical industry. Due to the fact that we could adapt to market requirements promptly and flexibly, many changes occurred in our manufacturing profile.
-
1996
We began to work together with SKF. We purchased our first brand new Hyundai lathes, and launched a serial production of parts for bearings.
-
1994
We invested some funds in our first second-hand, numerically controlled CNC machine tools. New machines, new technology, new efficiency of production. We started to make our first steps on the European market.
-
1984
It all started with a small workshop that was opened by the Company’s present owner and CEO, Jan Stańczyk. We had two employees and second-hand traditional lathes and presses. We used to produce mainly automotive parts for the spare parts market.
Place your stakes on an experienced, reliable CNC company,
the one you can trust.
What is primarily important for us is a long-standing cooperation, which can be confirmed by the global Customers we have been working with to-date.
Set the standards in your industry together with us.