Press brakes are the devices – most often hydraulic – used to mechanically (and in controlled conditions) change the shape of the material, usually some type of sheet made out of metal. Although the mechanism is pretty straightforward (uses a natural plasticity of material and deforms it with sheer force), the requirements for contemporary manufacturing processes highlight the need for precision and repeatability of press brakes. The introduction of numerical control allows such devices to answer such needs, thus – shortening the time required to manufacture even big batches of bent parts and elements.
What is a press break and how does it work?
Press brake is a device for mechanically changing the shape of materials in the spectrum of their plasticity; most often cold, but some of these devices can execute that process hot. To bend materials – mainly sheets – are used hydraulic actuators that can be controlled manually (eg. with limiters or templates) or numerically, with the usage of CNC. It is worth mentioning that cold press break processing uses natural plasticity; hot processes use temperature to increase the forming potential of machined material.
Press brakes are used to manufacture parts for the following applications:
- a vast variety of sheets – mainly metal, eg. to cover buildings,
- a vast variety of devices chassis (eg. computers and home appliances),
- body parts for cars,
- and many, many more.
Although press breaks (computer numerically controlled and automatic) are connected mainly with forming metal sheets, can bend other materials, such as:
- polymers (especially high performing),
- composites (eg. glass fiber and aluminum, often used in the aviation industry),
- after additional processing – other materials.
Press brake machine – as a device – combines a few key parts that can help to achieve the wanted shape of bend:
- the key element of most press breaks is a hydraulic pump that generates the kinetic force required to change the shape of an object,
- bending beams – parts that are transferring such force – via actuators – on the machined part. In addition – these are the elements that can regulate the final depth and length of the bend radius,
- modern press breaks (CNC and automatic) often use feeding systems that allow for increased work speed or complete automatization,
- stamps and templates/matrixes – the automatic press breaks (manually controlled) often use these elements to increase the efficiency of bending machine work,
- CNC controller – the numerically controlled press brake requires some type of computer device to execute steps of the process (from feeder to systems that remove bent parts from the working area).
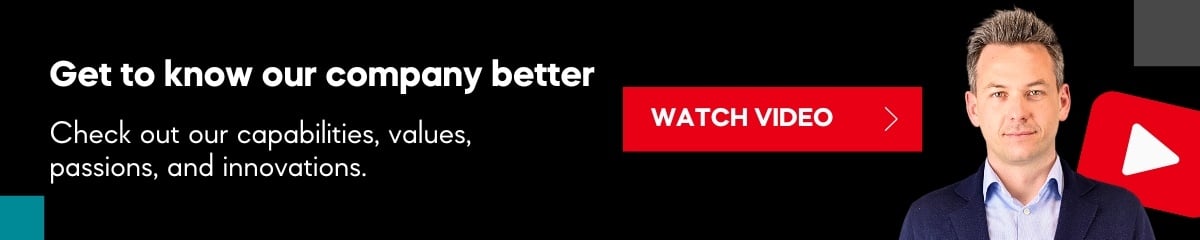
How does the press brake work
Just like in the case of machining devices, almost every device has its numerically controlled counterpart. Both types of these devices use the same method of removing material, but they differ in the type of control. The case with the press brake machine is identical – the idea of bending parts has been known for ages and evolved over the years. Hydraulic actuators increased the speed and capacity of work, but numerically controlled systems allowed further automatization of work.
Executed by contemporary press brakes process of bending looks almost identical to CNC and traditional devices:
1. formed material is put in the working area,2. limiters (matrix, template, or automatized feeders) place material in the wanted place (X-axis),
3. bending beams, placed in wanted places – to achieve the expected depth and length of bend (Y1 and Y2 axes) move accordingly to the given parameters to achieve expected results, with material plasticity in mind (R axis),
4. after the bending process material is moved further, sometimes cut with additional tools, by bumper fingers in axises Z1 and Z2,
5. the process repeats till the end of the job.
Mentioned machining is important because press brakes often bend already milled or turned material; such processes are easier to perform on a more 'flat' surface. That is why press brakes are often one of the more important devices in the machine park of CNC plants, such as RADMOT.
Press brake: numerical and traditional – what are the differences?
The fundamental difference between these two types of press brake lies in the controlling agent and the potential to repeatedly bend material. Automatized presses – most often – can execute one type of bend in one particular setting. That makes these devices perfect for the production of bent steel sheets and other materials with repeatable and consistent shapes.
Adding another bend requires changing settings on the press or moving to another device, but both of these actions require time and effort on the side of the operator.
To achieve such 'multiple bending capacity' there are required lines of press brakes to create an actual 'bending line': first device creates bend A, second – bend B, etc. Numerically controlled press brakes can execute the whole bending process in one device and one working area which excludes the possibility of bad mountage on another working area and provides precision for each bend. That translates to efficiency of manufacturing, especially combined with automatized feeders and receivers.
One order, many benefits – this is how you collaborate with RADMOT
At RADMOT, we offer CNC milling services, CNC turning services, as well as many additional services, including washing, aluminum anodizing, laser marking and assembly. We have at your disposal over 80 modern machines in our machine park, all from renowned manufacturers. Download the presentation and check on which machine tools we produce CNC turned parts and CNC milled parts.
Contact us and tell us what you need. We have been providing CNC services for almost 40 years. Our valuation is completely free. And if you're in doubt about which technology will work best for you, our expertise is at your service.